Electric and general update:
The final plumbing was done last Monday and electric was on Tuesday. That was a mistake not leaving a day between the trades. I didn't have anyone lined up to backfill at the pad so I did it myself. I started at 6am Tuesday morning and it took me about 3 hours to place 2" of sand on top of the plumbing and then the soil up to grade. I'm guessing I moved 2-3 tons of material. I'm glad I did it, they would not have been able to do the work, with the mounds of soil in front of the panel and on the pad. Before and after pic (I didn't spend time grading since the equipment pad screening wall will dig up the area again).
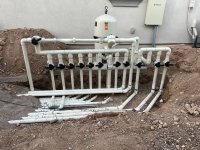
Electricians sent a crew of 4, which included one new tech who was learning on the job. They were watching over him fairly closely so I didn't mind. I think the flex to the light transformer and some of the wiring in the 120V compartment could have been installed a little cleaner, but it's not bad.
Flex install
Here is a pic of their guy installing the 1.5” threaded coupling for the microbrite.
Intellicenter & closer view of the 120V compartment

I had them run a 70amp circuit (they ran #4) so I'm set up at the Intellicenter for a heat pump if I ever decide to put one in.
I've got my equipment pad light installed (that was $230 for 16' of RMC, wire, and mount the box and light) wired to one of the relays (for now). While I'm entirely comfortable wiring and mounting electrical fixtures, my rigid conduit bending skills aren't that good. I originally thought I wanted a breaker for the pad light but the electrician said his boss would not be happy if they wired it up that way. Anyone know why that is? I didn't care that much so I let him wire it to the relay. It's an easy fix if I want to switch it to a breaker later.
I asked about bonding the pump when they were nearly finished and they said they'd get to it. After they left I looked it over and found they missed it but did bond the panel.

I'm befuddled how contractors that do this work every day can miss this stuff. They could really use some attention to QC. Called them back and they came the next day to fix.


The entire job took a couple hours and seems like they did a good job overall.
Had final plumbing and electric inspection on Friday and all passed! Yipee!! Only inspection left is pre-plaster.
Finalizing fence contractor now. I'm not in a rush now since my landscaper still has over a month before they start and they have about 2 months of work. Funny that I called the permit processing person to see if I need a permit for the fence, they said I did. I go on their website to submit it and it clearly says permit not needed for a residential fence under 7' tall. I submitted it anyway, we'll see what they say.
Working through the door and window barrier installations. As a follow-up from
this earlier post, I found out that Buckeye still requires the barriers regardless of whether I have anyone under 6 years old living here or not. Oh well, worth a try. Found out I can get locks for my new Pella windows that can be installed to meet barrier requirements. Now I'm nailing down which one(s) are fire egress windows from the bedroom as those don't get the locks. I've got three windows that open from the master bedroom out to the pool area. Two are large that meet the requirements for fire egress, so I'm asking the inspector to confirm if both should be left without barriers. I'm going to have to get someone to install the autoclose/autolatch on the oxxo sliding door. I've got emails into the permitting department but from what I understand, Buckeye doesn't allow alarms instead of autoclose/locks.