- Oct 25, 2015
- 5,822
- Pool Size
- 28000
- Surface
- Plaster
- Chlorine
- Salt Water Generator
- SWG Type
- CircuPool RJ-60 Plus
Folks,
***** EDIT*****
With some great input from our experts I should state up front I've greatly over-simplified this in my initial post by omitting the rest of the system behavior. If you're interested in how this affects pressure and flow through your system read on for some excellent information provided by TFP experts. If like most, you really don't care about this you can just follow @JamesW simplified advice and just put the largest impeller in your pump that the motor can power. But if you care at all you should read all their posts. They're a fantastic explanation with some great insight into your pool's hydraulic behavior.
*****EDIT*****
Since changing to a VS motor I noticed my pool was getting a little dirtier on the bottom than it used to be. I use a suction cleaner and it was now running way too slow unless I speed up to get the wheel speed to specification. I initially thought this would be an easy fix by setting an additional cycle at higher speed but I also remembered @JamesW had indicated I might be able to go up a size on my impeller size. My pump is a Jandy FHPM-1.0 and the next size up is a FHPM 1.5. I looked into this a little further and found next size up is only slightly bigger but would significantly improve flow while staying below the 1.65 HP rating of my new V-Green motor. Here's the pump curve:

Looks like I could get surprisingly better flow from this small change in impeller size (20 gpm to 35 gpm). Looking at the pump body and parts diagrams I figured out there is a wide range of impellers that will fit and there are two different diffuser sizes. My impeller was the largest size for the diffuser so I had to go up on that as well. Another huge advantage is at the high speed. Look at what happens at 3450 rpm curve:

I go from just under 50 gpm to just under 80 gpm. Of course this isn't exactly right since the increased flow will increase pressure drop in the filter and actually result in a slightly higher pressure. But this is one of the nice things about having a filter that is over-sized. The pressure doesn't really go up much:
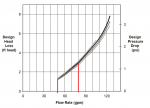
As you can see my filter is sized such that I'm on the very bottom of the pressure drop curve so going up to about 80 gpm only increases my drop by about 1.5 psi.
So bottom line, when you change just the motor to convert a VS pump it's definitely well worth looking into the impeller size. I've noticed our experts mention many times that when you buy the entire pump a big advantage is that the impeller is optimized for the motor. I think this little exercise proves the point. Even with no impeller change you can still save a lot of operating cost with just the VS motor only approach. But when you want the maximum savings and performance it's a real good practice to look at the whole system, the pump motor, impeller and filter to get the best overall performance. Since I was at the top end of the diffuser my cost was double that of an impeller change but still only $70 so the motor and impeller change totaled $470. Still way lower than a complete pump. To me this also illustrates a huge benefit of having TFP around for ordinary pool owners. It might be difficult for a handy DIY type pool owner to figure this out and I doubt that many pool service companies would do this. Even if they did costs would be prohibitive. TFP has experts that can help guide anybody that's reasonably handy to do this themselves.
I hope this is helpful to others considering an upgrade to a VS motor while using their existing pump.
Chris
***** EDIT*****
With some great input from our experts I should state up front I've greatly over-simplified this in my initial post by omitting the rest of the system behavior. If you're interested in how this affects pressure and flow through your system read on for some excellent information provided by TFP experts. If like most, you really don't care about this you can just follow @JamesW simplified advice and just put the largest impeller in your pump that the motor can power. But if you care at all you should read all their posts. They're a fantastic explanation with some great insight into your pool's hydraulic behavior.
*****EDIT*****
Since changing to a VS motor I noticed my pool was getting a little dirtier on the bottom than it used to be. I use a suction cleaner and it was now running way too slow unless I speed up to get the wheel speed to specification. I initially thought this would be an easy fix by setting an additional cycle at higher speed but I also remembered @JamesW had indicated I might be able to go up a size on my impeller size. My pump is a Jandy FHPM-1.0 and the next size up is a FHPM 1.5. I looked into this a little further and found next size up is only slightly bigger but would significantly improve flow while staying below the 1.65 HP rating of my new V-Green motor. Here's the pump curve:

Looks like I could get surprisingly better flow from this small change in impeller size (20 gpm to 35 gpm). Looking at the pump body and parts diagrams I figured out there is a wide range of impellers that will fit and there are two different diffuser sizes. My impeller was the largest size for the diffuser so I had to go up on that as well. Another huge advantage is at the high speed. Look at what happens at 3450 rpm curve:

I go from just under 50 gpm to just under 80 gpm. Of course this isn't exactly right since the increased flow will increase pressure drop in the filter and actually result in a slightly higher pressure. But this is one of the nice things about having a filter that is over-sized. The pressure doesn't really go up much:
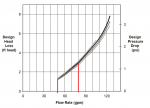
As you can see my filter is sized such that I'm on the very bottom of the pressure drop curve so going up to about 80 gpm only increases my drop by about 1.5 psi.
So bottom line, when you change just the motor to convert a VS pump it's definitely well worth looking into the impeller size. I've noticed our experts mention many times that when you buy the entire pump a big advantage is that the impeller is optimized for the motor. I think this little exercise proves the point. Even with no impeller change you can still save a lot of operating cost with just the VS motor only approach. But when you want the maximum savings and performance it's a real good practice to look at the whole system, the pump motor, impeller and filter to get the best overall performance. Since I was at the top end of the diffuser my cost was double that of an impeller change but still only $70 so the motor and impeller change totaled $470. Still way lower than a complete pump. To me this also illustrates a huge benefit of having TFP around for ordinary pool owners. It might be difficult for a handy DIY type pool owner to figure this out and I doubt that many pool service companies would do this. Even if they did costs would be prohibitive. TFP has experts that can help guide anybody that's reasonably handy to do this themselves.
I hope this is helpful to others considering an upgrade to a VS motor while using their existing pump.
Chris
Last edited: