Although relatively new to TFP, we’ve already learned a lot from this site. Everyone here seems very helpful and knowledgeable, so hopefully some of you can offer good renovation/contractor recommendations.
We have a Sylvan ~22K gal IG gunite pool that is painted; no plaster, tile, or coping, just painted gunite with a wet-laid bluestone deck. The attached pictures should help to clarify. The house/pool was built in 1976 (46 years old) and we have owned it for 21 years. Other than adding a newer Jandy controller and heater about 15 years ago, we have not painted or invested in any improvements to the pool other than normal equipment maintenance/replacement. Overall, the paint has held up well but it is now worn through in some areas with significant (~1/4”) etching of the gunite shell in the deep end (can be seen in "Pool Overall" photo). The pool works OK and we use it every year, but it’s really starting to show its age, so it’s time for an upgrade.
We’re located in Northern NJ (Mendham) and would greatly appreciate recommendations for good pool contractors in our area. Our renovation timeframe is very flexible. For us, cost and timeline are less important than finding a contractor who takes pride in their work and can do a good job.
Regarding the renovation, since the pool is currently just a painted shell, and re-painting doesn’t seem to be a realistic option
, I assume the pool will need new coping, tile, and plaster. As the bond beam is currently level with the top of the deck (see photos), I also assume the level of the deck will need to be raised to match the level of the new coping. All of this will likely add up to a lot of $$$, so any lower cost alternatives that anyone can suggest would also be greatly appreciated.
Thanks in advance for any suggestions that you may have.

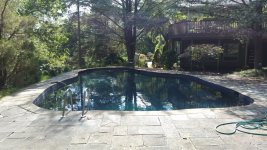


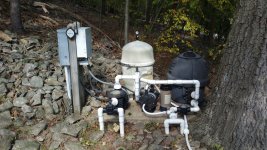
We have a Sylvan ~22K gal IG gunite pool that is painted; no plaster, tile, or coping, just painted gunite with a wet-laid bluestone deck. The attached pictures should help to clarify. The house/pool was built in 1976 (46 years old) and we have owned it for 21 years. Other than adding a newer Jandy controller and heater about 15 years ago, we have not painted or invested in any improvements to the pool other than normal equipment maintenance/replacement. Overall, the paint has held up well but it is now worn through in some areas with significant (~1/4”) etching of the gunite shell in the deep end (can be seen in "Pool Overall" photo). The pool works OK and we use it every year, but it’s really starting to show its age, so it’s time for an upgrade.
We’re located in Northern NJ (Mendham) and would greatly appreciate recommendations for good pool contractors in our area. Our renovation timeframe is very flexible. For us, cost and timeline are less important than finding a contractor who takes pride in their work and can do a good job.
Regarding the renovation, since the pool is currently just a painted shell, and re-painting doesn’t seem to be a realistic option
Thanks in advance for any suggestions that you may have.


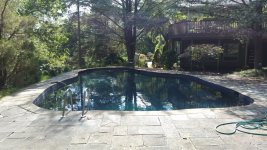


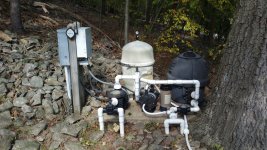
Last edited by a moderator: