- Oct 25, 2015
- 5,151
- Pool Size
- 25000
- Surface
- Plaster
- Chlorine
- Salt Water Generator
- SWG Type
- CircuPool RJ-60 Plus
Folks,
*** Edited to provide a You-Tube link that should be helpful.***
As some of you know I zapped my electronics to my Jandy pool using heater and can't seem to fix it. Everything points toward a problem with the fan speed. Since it's enclosed in a housing there's no way to use a light beam reflective type of rpm measurement. So I was thinking about using a Fourier's transform technique to calculate it. Thought I was in for a dive into my 45 old math books when I did a little Googling and found there's now an app for that! Yep, and it seems to work great. You download this app called Spectrum Analyzer App (I think there are a few other's that may work but I haven't tested them). Then you start the app with the fan running. In a few minutes you gather the spectrum data and can see the fundamental frequency in HZ. Divide by the number of blades (in my case 11) then multiply by 60 to get rpm. In my case the fundamental freq is about 430 (you can tell it's the fundamental frequency because there are repeated harmonics of this peak further on the right of the spectrum) then divide by 11 and multiply by 60 and I get 2345 rpm. Well below the rated speed of 3480 stamped on the motor. So something happened when I dumped a cup of water on the power distribution board right on the fan wires that messed the fan up too. Here's a You-Tube link that takes you to a demonstration of the technique. I've verified some of the measurements that he demonstrates with my android phone. Here's a screenshot of the spectrum that I used:
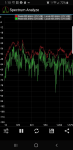
I have tried everything else that could be the problem and tested or replaced the components that proved defective. You can see the details of that in my heater repair thread. But I thought it would be better to put this thread up separately in case somebody searches for this with a more descriptive title. Moderator, if you'd rather put this somewhere else please do your magic and move to the appropriate spot.
I hope this helps somebody else.
Chris
*** Edited to provide a You-Tube link that should be helpful.***
As some of you know I zapped my electronics to my Jandy pool using heater and can't seem to fix it. Everything points toward a problem with the fan speed. Since it's enclosed in a housing there's no way to use a light beam reflective type of rpm measurement. So I was thinking about using a Fourier's transform technique to calculate it. Thought I was in for a dive into my 45 old math books when I did a little Googling and found there's now an app for that! Yep, and it seems to work great. You download this app called Spectrum Analyzer App (I think there are a few other's that may work but I haven't tested them). Then you start the app with the fan running. In a few minutes you gather the spectrum data and can see the fundamental frequency in HZ. Divide by the number of blades (in my case 11) then multiply by 60 to get rpm. In my case the fundamental freq is about 430 (you can tell it's the fundamental frequency because there are repeated harmonics of this peak further on the right of the spectrum) then divide by 11 and multiply by 60 and I get 2345 rpm. Well below the rated speed of 3480 stamped on the motor. So something happened when I dumped a cup of water on the power distribution board right on the fan wires that messed the fan up too. Here's a You-Tube link that takes you to a demonstration of the technique. I've verified some of the measurements that he demonstrates with my android phone. Here's a screenshot of the spectrum that I used:
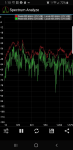
I have tried everything else that could be the problem and tested or replaced the components that proved defective. You can see the details of that in my heater repair thread. But I thought it would be better to put this thread up separately in case somebody searches for this with a more descriptive title. Moderator, if you'd rather put this somewhere else please do your magic and move to the appropriate spot.
I hope this helps somebody else.
Chris
Attachments
Last edited: