- Jun 5, 2020
- 152
- Pool Size
- 18000
- Surface
- Plaster
- Chlorine
- Salt Water Generator
- SWG Type
- CircuPool RJ-60 Plus
We bought a house that had a pool 4 years ago, and have been managing it ourselves ever since. We've been thinking about adding a SWG for the last year or so and this spring as the chlorine demand started to rise, we decided it was time to make it happen.
My initial plan was to hire someone to install it. I tried to get estimates and most companies weren't interested. The few that came out never got back to me with pricing. As I read more and more on this site, I started to realize I might be able to do this myself. So, over the last couple of months I started working on a plan to update our pool plumbing and install a SWG. I read every post on the subject going back a few years and benefited from almost every one. I started out as a novice and now feel like [whatever 1 step above a novice is]. I hope some people out there can benefit from reading about my experience.
As I read through posts here, I quickly realized Circupool was the best SWG choice for me. They'll still honor the warranty even though a pro didn't install it. Plus it seemed like a high quality product. I considered both the RJ45 and RJ60. The 60 can produce 50% more chlorine per day than the 45 for about 20% more money, so that was the deciding factor for me. Even though I plan to run the filter pump 24 hours a day, It's nice to know that I *could* run the pump less than half the day if I wanted, and still produce enough chlorine.
The first phase of the project was to enable spillover control. This has been on my project list for several years now. The way our pool was plumbed, water spilled over from the spa to the pool whenever the filter pump was running in pool mode. There was a check valve preventing back-flow from the spa to the pool when the pump was off, but no way to shutoff the flow. The existing plumbing didn't have space to add anything, so I needed to remove/replace the plumbing. Here's the "before" pic (each photo in this post is a thumbnail that you can click on for a larger pic):
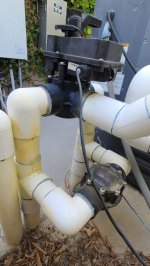
Phase 1 - Spillover plumbing
I had worked quite a bit with ½-1" PVC on irrigation and electrical projects over the years, but never with PVC this large. I had always used those ratcheting pipe cutters. But, I had read that those perform poorly with larger sizes. So, being a beginner, I was not sure what I should use to cut. I eventually realized that most any saw will work. For my cuts into existing plumbing, I used a hand-held hacksaw. At first I tried using a 32 tooth-per-inch blade, but it was a lot of work. The 18 tpi blade worked much better for me, and just required some light sanding after the cut. For the new PVC, I used my table saw to cut it; that is overkill, but made nice smooth precise cuts.
The actual plumbing was fairly straight-forward. I used pipe extenders from my local pool store (similar to these that have been posted many times) after cutting off the existing plumbing. I used a cheap Home Depot shutoff valve. I considered using a higher quality Jandy valve, but I expect the valve to be used rarely (if ever). I had a minor issue with the 3 way valve leaking which I brought up in this thread. But, that problem was resolved as discussed there. Here is a photo of the end result:

I wish it wasn't quite so messy looking, but I should've been more careful with my rags I used to wipe down after each connection.
Phase 2 - Electrical
The first issue to be addressed was that all of the relays in our automation panel were being used. We needed to free one up so that we could flip the DIP switch to enable spillover mode. Our spa and pool lights were on separate relays. At first I was going to combine them onto one relay, but I decided to free up both relays and add a Wifi switch to control each light. So far, that wifi switch has worked great and since 2 relays were freed up, we have a remaining spare relay after enabling spillover mode. I may use that to control an acid pump if we decide to add one of those. I removed the GFCI outlet that protected the pool/spa lights and put the wifi switch in its place. I converted the circuit breaker powering the lights to a GFCI breaker, which is also used to power/protect the SWG.
We have a variable speed pump which is not connected to the filter pump relay (it's powered directly from the breaker, and the automation signals one of 4 preset speeds over low voltage wiring). Being a newbie, I was concerned that the automation wouldn't switch the filter pump relay since it knew that the pump wasn't connected to it anymore, but happily discovered that the relay still switches. So I was able to use that to switch the SWG power on/off as the filter pump was turned on and off. I ran conduit from my panel out to a spot near the SWG wall box and added an electrical box with an outlet to plug the SWG into (and also an acid pump if we ever decide to add that). Power to the outlet is switched on and off by the filter pump relay. I had to add a 3 prong plug to the end of the Circupool power cable, which I got at Home Depot.
Phase 3 - SWG plumbing
Here's a "before" pic looking from above, the heater outlet is on the right, and the 3 way Jandy valve on the left is the return:

As you can see, there was not room to add anything. I considered rotating the heater to allow more space for the plumbing, but elected not to do that because it would have required re-plumbing the gas connection, and all of the other orientations had problems of one sort or another. Moving the heater might have helped, but there was nowhere practical to move it to. So, I considered that side of plumbing to be in a fixed place. The other end with the 3-way Jandy valve was also fixed because I couldn't come up with a better solution without a wholesale redesign of all the plumbing. Another issue was that the 3 way valve inlet and heater outlet are at different levels. Also, when the 3 way valve was installed it was oriented so that it angled down just slightly. It wasn't even noticeable with the original install, but the pipe length with the SWG made the slope obvious. I also thought about adding a heater bypass discussed often on this site, but decided it wasn't worth the added complexity. After months of thinking about layouts and reading posts on this site I came up with a solution:

The first breakthrough in planning the layout was figuring out that the 3 way Jandy valve would accept a 2½ inch adapter (note that it takes an adapter not a 2½ inch pipe) around the outside of the inlet (thanks to multiple people here who have posted that info in several threads over the last few years). So I was able to cut the existing plumbing flush with the valve inlet and glue a 2½ inch-to-2 inch adapter there. The adapter was a little tricky to find...it's available online, but a local plumbing supply store carried it, which is where I bought it. The other end of the plumbing connected to the heater outlet. As a novice, I had a hard time figuring out what to use there. I eventually discovered that it's a proprietary Raypak (my heater manufacturer) part. I downloaded the manual for the heater and found the part number in there. It was available online, but my local pool supply shop was able to order it for me quicker for a similar price. The 90° elbow that is connected to the heater union is a "spigot" on one side and a "socket" on the other (aka a "street elbow" like this one I bought at my local Lowe's), which allowed the tight turn I needed from the heater. Being a beginner, this was something else I didn't know existed. This site was helpful in understanding the various PVC end types.
The straight pipe segment into the SWG flow switch is 10". I planned for 12", but there wasn't enough space for the wider flow switch to fit around the existing plumbing. The basic 2" pipe barely fit. It took some time and thought to figure out what order to glue all of the pipes/fittings. The final connection I made was the union to the SWG on the heater side, which I was able to precisely fit against the SWG while the glue began to set. By building out from each "end" I was able to account for the different levels and slope along the way. The SWG is inverted as recommended by Circupool with VSPs, and I thought that would be better since it slopes up a bit from one side to the other. The fitting between the SWG and Jandy valve is for the possible acid pump addition (thanks for suggesting that in the other thread). With all the connections involved, I was nervous about something leaking. Luckily it didn't! I did wait 12 hours before pressure testing since the heater union and Jandy valve are CPVC, and I just used the regular medium blue cement with primer on each joint.
If I could go back in time and do the project over again I might redo the plumbing to the heater inlet, but I didn't think about that as much as I should have beforehand.
I did my first pool salt test and was surprised that it was 2600ppm before adding anything. The pool was filled less than 2 years ago, so I guess that salt is from liquid chlorine and from the softened fill water we use (although I tested our softened water and it doesn't even register 200ppm). So, I only needed to add 3 bags of water softener salt crystals (I used these bags of salt) to bring our salt level to 3400 ppm. I gave the salt a day to mix and then turned on the SWG. So far it seems to be working great. It's set at 30%, and will run 24 hours. FC is a little above target and very slowly drifting down. I'll probably bring the CYA up a little more, and might be able to get the SWG turned down to 25 or 20%. The lowest speed of my variable speed pump is 1100 rpm...even that was able to close the SWG flow switch. I added 100 rpm to that lowest speed and will have the pump run all the time at 1200, which the pump says uses about 100 watts. Now that I can control spillover, I hope I can bring my TA down some and find a nice pH spot that only requires fairly infrequent acid additions. Otherwise, my acid pump project is next!
Again, thanks to everyone who posted their projects in the past; I really benefited from it. I hope a few people find my story helpful and if anyone thinks I made mistakes please let me know!
My initial plan was to hire someone to install it. I tried to get estimates and most companies weren't interested. The few that came out never got back to me with pricing. As I read more and more on this site, I started to realize I might be able to do this myself. So, over the last couple of months I started working on a plan to update our pool plumbing and install a SWG. I read every post on the subject going back a few years and benefited from almost every one. I started out as a novice and now feel like [whatever 1 step above a novice is]. I hope some people out there can benefit from reading about my experience.
As I read through posts here, I quickly realized Circupool was the best SWG choice for me. They'll still honor the warranty even though a pro didn't install it. Plus it seemed like a high quality product. I considered both the RJ45 and RJ60. The 60 can produce 50% more chlorine per day than the 45 for about 20% more money, so that was the deciding factor for me. Even though I plan to run the filter pump 24 hours a day, It's nice to know that I *could* run the pump less than half the day if I wanted, and still produce enough chlorine.
The first phase of the project was to enable spillover control. This has been on my project list for several years now. The way our pool was plumbed, water spilled over from the spa to the pool whenever the filter pump was running in pool mode. There was a check valve preventing back-flow from the spa to the pool when the pump was off, but no way to shutoff the flow. The existing plumbing didn't have space to add anything, so I needed to remove/replace the plumbing. Here's the "before" pic (each photo in this post is a thumbnail that you can click on for a larger pic):
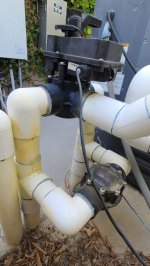
Phase 1 - Spillover plumbing
I had worked quite a bit with ½-1" PVC on irrigation and electrical projects over the years, but never with PVC this large. I had always used those ratcheting pipe cutters. But, I had read that those perform poorly with larger sizes. So, being a beginner, I was not sure what I should use to cut. I eventually realized that most any saw will work. For my cuts into existing plumbing, I used a hand-held hacksaw. At first I tried using a 32 tooth-per-inch blade, but it was a lot of work. The 18 tpi blade worked much better for me, and just required some light sanding after the cut. For the new PVC, I used my table saw to cut it; that is overkill, but made nice smooth precise cuts.
The actual plumbing was fairly straight-forward. I used pipe extenders from my local pool store (similar to these that have been posted many times) after cutting off the existing plumbing. I used a cheap Home Depot shutoff valve. I considered using a higher quality Jandy valve, but I expect the valve to be used rarely (if ever). I had a minor issue with the 3 way valve leaking which I brought up in this thread. But, that problem was resolved as discussed there. Here is a photo of the end result:

I wish it wasn't quite so messy looking, but I should've been more careful with my rags I used to wipe down after each connection.
Phase 2 - Electrical
The first issue to be addressed was that all of the relays in our automation panel were being used. We needed to free one up so that we could flip the DIP switch to enable spillover mode. Our spa and pool lights were on separate relays. At first I was going to combine them onto one relay, but I decided to free up both relays and add a Wifi switch to control each light. So far, that wifi switch has worked great and since 2 relays were freed up, we have a remaining spare relay after enabling spillover mode. I may use that to control an acid pump if we decide to add one of those. I removed the GFCI outlet that protected the pool/spa lights and put the wifi switch in its place. I converted the circuit breaker powering the lights to a GFCI breaker, which is also used to power/protect the SWG.
We have a variable speed pump which is not connected to the filter pump relay (it's powered directly from the breaker, and the automation signals one of 4 preset speeds over low voltage wiring). Being a newbie, I was concerned that the automation wouldn't switch the filter pump relay since it knew that the pump wasn't connected to it anymore, but happily discovered that the relay still switches. So I was able to use that to switch the SWG power on/off as the filter pump was turned on and off. I ran conduit from my panel out to a spot near the SWG wall box and added an electrical box with an outlet to plug the SWG into (and also an acid pump if we ever decide to add that). Power to the outlet is switched on and off by the filter pump relay. I had to add a 3 prong plug to the end of the Circupool power cable, which I got at Home Depot.
Phase 3 - SWG plumbing
Here's a "before" pic looking from above, the heater outlet is on the right, and the 3 way Jandy valve on the left is the return:

As you can see, there was not room to add anything. I considered rotating the heater to allow more space for the plumbing, but elected not to do that because it would have required re-plumbing the gas connection, and all of the other orientations had problems of one sort or another. Moving the heater might have helped, but there was nowhere practical to move it to. So, I considered that side of plumbing to be in a fixed place. The other end with the 3-way Jandy valve was also fixed because I couldn't come up with a better solution without a wholesale redesign of all the plumbing. Another issue was that the 3 way valve inlet and heater outlet are at different levels. Also, when the 3 way valve was installed it was oriented so that it angled down just slightly. It wasn't even noticeable with the original install, but the pipe length with the SWG made the slope obvious. I also thought about adding a heater bypass discussed often on this site, but decided it wasn't worth the added complexity. After months of thinking about layouts and reading posts on this site I came up with a solution:

The first breakthrough in planning the layout was figuring out that the 3 way Jandy valve would accept a 2½ inch adapter (note that it takes an adapter not a 2½ inch pipe) around the outside of the inlet (thanks to multiple people here who have posted that info in several threads over the last few years). So I was able to cut the existing plumbing flush with the valve inlet and glue a 2½ inch-to-2 inch adapter there. The adapter was a little tricky to find...it's available online, but a local plumbing supply store carried it, which is where I bought it. The other end of the plumbing connected to the heater outlet. As a novice, I had a hard time figuring out what to use there. I eventually discovered that it's a proprietary Raypak (my heater manufacturer) part. I downloaded the manual for the heater and found the part number in there. It was available online, but my local pool supply shop was able to order it for me quicker for a similar price. The 90° elbow that is connected to the heater union is a "spigot" on one side and a "socket" on the other (aka a "street elbow" like this one I bought at my local Lowe's), which allowed the tight turn I needed from the heater. Being a beginner, this was something else I didn't know existed. This site was helpful in understanding the various PVC end types.
The straight pipe segment into the SWG flow switch is 10". I planned for 12", but there wasn't enough space for the wider flow switch to fit around the existing plumbing. The basic 2" pipe barely fit. It took some time and thought to figure out what order to glue all of the pipes/fittings. The final connection I made was the union to the SWG on the heater side, which I was able to precisely fit against the SWG while the glue began to set. By building out from each "end" I was able to account for the different levels and slope along the way. The SWG is inverted as recommended by Circupool with VSPs, and I thought that would be better since it slopes up a bit from one side to the other. The fitting between the SWG and Jandy valve is for the possible acid pump addition (thanks for suggesting that in the other thread). With all the connections involved, I was nervous about something leaking. Luckily it didn't! I did wait 12 hours before pressure testing since the heater union and Jandy valve are CPVC, and I just used the regular medium blue cement with primer on each joint.
If I could go back in time and do the project over again I might redo the plumbing to the heater inlet, but I didn't think about that as much as I should have beforehand.
I did my first pool salt test and was surprised that it was 2600ppm before adding anything. The pool was filled less than 2 years ago, so I guess that salt is from liquid chlorine and from the softened fill water we use (although I tested our softened water and it doesn't even register 200ppm). So, I only needed to add 3 bags of water softener salt crystals (I used these bags of salt) to bring our salt level to 3400 ppm. I gave the salt a day to mix and then turned on the SWG. So far it seems to be working great. It's set at 30%, and will run 24 hours. FC is a little above target and very slowly drifting down. I'll probably bring the CYA up a little more, and might be able to get the SWG turned down to 25 or 20%. The lowest speed of my variable speed pump is 1100 rpm...even that was able to close the SWG flow switch. I added 100 rpm to that lowest speed and will have the pump run all the time at 1200, which the pump says uses about 100 watts. Now that I can control spillover, I hope I can bring my TA down some and find a nice pH spot that only requires fairly infrequent acid additions. Otherwise, my acid pump project is next!
Again, thanks to everyone who posted their projects in the past; I really benefited from it. I hope a few people find my story helpful and if anyone thinks I made mistakes please let me know!