Hello, I see from other posts that this isn't uncommon. I'm hoping this community can help us decide what to do. All 37 segments of new pour in place coping had a stress crack near the middle of the segment, starting at the bullnose and ranging from 6" to the full width, within three months. We aren't construction savvy enough to know if this was the result of a poor mix, humidity, or a problem with the expansion joints. The company is local, reputable, fully licensed, and been in business since the 70's. We have been attempting to get them to come evaluate the cracks since June. They say they can come look at them next week, but all they can do is "fill in all those regions with the same color cement". They're saying "all pour in place concrete cracks". We are skeptical that this isn't a bigger issue given how quickly the cracks appeared and that every single segment cracked in an almost uniform way. (This company also defaced the entire length of our coping with a power washer on the last day of construction, and then the wire brush used to attempt to fix that issue with an acid wash fell apart and hundreds of little wire bristles rusted to the bottom of the brand new white plaster and were scattered all over the decking. We considered both of those issues sort of fixed to the best of their ability, but we no longer trust them.) Should we: A. Drop the whole thing and live with the cracks B. Have them come and do what sounds like a cosmetic fix, which will likely make where the cracks are more visible/ugly or C. Immediately file a complaint with the Contractors State Licensing Board and hope they send an expert to evaluate if the work is up to industry standard or not and require the contractor to remedy any substandard work. We took out a home loan to renovate this pool and it's heartbreaking that it's been one issue after the other, and for the cost it should have looked good for longer than a month or two. I will include photos of the wire bristles and the power washer marks just for reference, and then a small selection of the coping cracks. Thank you in advance for any advice or options you have, we truly appreciate you taking the time.

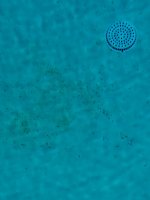

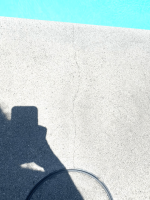



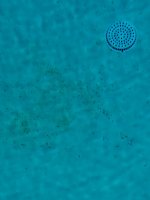

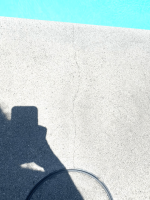

