I'm nearly over the finish line with my recent pool renovation so this is more of a retrospective than a play-by-play. I'm thinking of calling this saga: In for a penny, in for a pound. By that I mean that once you start fixing one thing, there can be an unexpected domino effect or chain reaction that creates something new to address (and dig into your wallet to cover) that you didn't anticipate! An alternate title for the saga: Pools are like onions... and "no" not because they stink but because they have layers. At least in my case, once I got through one thing, another one would surface -- sometimes caused by something that preceded it and sometime it was there all along and I just didn't understand the complexity of things. So, it's been a learning journey for sure. I have few true regrets but a few avoidable lessons. One important thing to think about is whether you need a GC (general contractor) / project manager for your job if the PB is not playing that role -- some do and some don't -- and whether you are willing and able to serve in that role. I ended up serving as a quasi-GC since I had to communicate with, coordinate, and separately pay the concrete contractor (who arranged the dumpster and concrete delivery), the pool contractor (who subbed out the chipping and replastering but did the pipe pressurizing, tile and equipment replacement himself), and the electrician to wire in the new heater and light transformer and remove the old pump timer. My job wasn't that big compared to some and I work from home so could deal with schedule changes pretty gracefully.
My story ...
In February this year, I bought my current 1989-built home with a 30'x15' pool that I think was built in about 2000 based on aerial photos and permit records. I had a pool inspection done before finalizing the deal on the house so I knew the pool had a few issues with aging, yet still functioning equipment and an aging, cracked aggregate deck. The house / property size and layout, and location met all my desires for a spot to garden, exercise my dogs, and locate my empty nest with rooms for visiting kids, family, friends, and AirBNB and/or Swimply guests. The pool was an exciting "perk" to go along with my retreat-ish vision and something I was willing to invest some time and money into beautifying and making into a year-round amenity for myself and others to enjoy. I had been looking for waterfront (either lake- or river-front property) so a pool seemed to fit my wish to look out on sparkling water.
The main issue with the pool deck / coping was that these had been poured as one piece rather than as separate pours or pieces. Further, there was an area where a section of the slab by the deep-end had sunk down on the yard side of the slab and tipped up on the coping side (a bit like a teeter totter) such that the coping was separated from the waterline tile by about 2" allowing moss and weeds to take root in the gap. On this same section, one of the two metal handrails for the ladder had broken off or rusted out leaving a jagged hole in the slab. In the two photos, you can see the hole where the grab rail used to be and attempts to repair cracks extending in two directions from the hole. In the wider angle photo you can see the white gap between the tile and coping along the side with the ladder, where the slab upheaval occurred. A secondary issue was that the deck was aggregate (among my least favorite surfaces to walk on barefoot). So, I knew something would need to be done about the deck.


Another important tidbit is that I'm in the Pacific Northwest (PNW) where the summers are very short, the rain falls 175 days of the year in my town, and the winters are fairly mild (seldom dipping below freezing). So, my plan for getting year-round use of the pool included getting a retractable pool enclosure made by Alukov much like the one in the photo below.

I did as much due dilligence as I could, which included but was not limited to getting quotes from several different manufacturers/dealers of different types of enclosures, checking wind and snow load in my area and county requirements, reading reviews on Houzz and FaceBook, getting drawings, and visiting a property owner in the PNW with a 10 year-old Alukov enclosure so I could see how they stand up to our climate. Once again, the concrete deck became a crucial focus as the foundation for this structure and not something one would want to try to address after enclosure installation.
In researching concrete companies, I was referred to the same local contractor (Tony at Absolutely Fine Concrete) by two parties who didn't know each other -- the owner of the Alukov enclosure I'd visited and the pool construction / maintenance company (KrisCo Pools) that did my pre-purchase inspection and later a one-on-one lesson on how to use/maintain my equipment, vacuum and adjust the water level in the pool, and test and balance my water. So, I contacted Tony to come out for a quote, had a second contractor (a friend of a friend) come out for a quote, and talked to a few others who either seemed skiddish about working around a pool or had other reasons they were not keen to come out for a quote.
Tony was the obvious choice based on his portfolio and track record and his connections with folks in the pool building industry in Seattle. We were initially slated to start the demolition May 1st until we ran into two or three snags: (1) We couldn't find a pool company to come out to put the pipes under pressure in the timeframe needed. This procedure is not in Tony's wheelhouse and not a step he was willing to skip given the risk of breaking a pipe during demolition. (2) When Krisco's expert came out to discuss the process and their availability with me and Tony, he noticed that there had been a second layer of tile glued over the top of the original tile, which meant the demolition process was most likely going to ruin the tile and mess up the plaster. So we now needed to find someone to re-tile the water line. (3) The existing plaster had been painted (at least once) and so it was highly recommended that the old plaster be chipped out and new plaster done. I could have taken a "wait and see" stance to see if the plaster would survive tile removal / replacement, but when I considered the logistics of doing a replaster a few years down the road with an enclosure already in place, it made the most sense to to do it now and be done with it.
Krisco was back up through August so it was looking like the whole project might be delayed until late summer, early fall or maybe 2025. Then, one of Tony's other pool contacts (Scott with the Gunite Company) wrapped up a big job in Bellingham a little early and had a window before his next big job (a 95' private pool new construction). So we were off to the races. Scott has turned out to be a godsend because he's been building pools for 30+ years, has a great personality, and I've learned a lot from him as we've worked through the quirks of my project. He's worked on a lot of pools in my local area and has a reputation for being transparent and more than fair.
Doing the tile and plaster increased the cost of the entire job by about 50% (half again as much as the concrete job) ... but I'm glad I committed to it. When we got the pool drained, I could see the paint was bubbling in a lot of places and likely covering up hidden plaster issues that would only worse with time and use. Also, with the mechanical failures of the old heater and pump, it's been great to have a PB who can help me with a good solution.
I've got lots of before, during and after photos and videos ... the one below shows the job after the old concrete was demolished and the plaster chipped out (done by two different vendors in parallel -- sharing the same dumpster) and after new concrete and coping pour was complete -- and after the waterline and step marker tile was laid but BEFORE plastering and refilling. Watching the plastering being done was like a cake being frosted - it was so cool to see the artistry involved!

The below photo was taken today. I'm still waiting for escutcheons for the new handrail. The new heater was fired up for the first time today and chemicals are about right! I'm looking forward to a swim as soon at the temperature's comfy (it's a chilly 60°F in Seattle today despite it still being August). The enclosure is slated for delivery and installation in late October / early November. Stay tuned. I hope to report on how well it retains heat. It will definitely cut down on bugs and debris in the pool!

In review, my pool's "face lift" that included

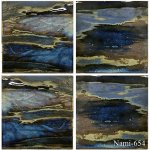


My story ...
In February this year, I bought my current 1989-built home with a 30'x15' pool that I think was built in about 2000 based on aerial photos and permit records. I had a pool inspection done before finalizing the deal on the house so I knew the pool had a few issues with aging, yet still functioning equipment and an aging, cracked aggregate deck. The house / property size and layout, and location met all my desires for a spot to garden, exercise my dogs, and locate my empty nest with rooms for visiting kids, family, friends, and AirBNB and/or Swimply guests. The pool was an exciting "perk" to go along with my retreat-ish vision and something I was willing to invest some time and money into beautifying and making into a year-round amenity for myself and others to enjoy. I had been looking for waterfront (either lake- or river-front property) so a pool seemed to fit my wish to look out on sparkling water.
The main issue with the pool deck / coping was that these had been poured as one piece rather than as separate pours or pieces. Further, there was an area where a section of the slab by the deep-end had sunk down on the yard side of the slab and tipped up on the coping side (a bit like a teeter totter) such that the coping was separated from the waterline tile by about 2" allowing moss and weeds to take root in the gap. On this same section, one of the two metal handrails for the ladder had broken off or rusted out leaving a jagged hole in the slab. In the two photos, you can see the hole where the grab rail used to be and attempts to repair cracks extending in two directions from the hole. In the wider angle photo you can see the white gap between the tile and coping along the side with the ladder, where the slab upheaval occurred. A secondary issue was that the deck was aggregate (among my least favorite surfaces to walk on barefoot). So, I knew something would need to be done about the deck.


Another important tidbit is that I'm in the Pacific Northwest (PNW) where the summers are very short, the rain falls 175 days of the year in my town, and the winters are fairly mild (seldom dipping below freezing). So, my plan for getting year-round use of the pool included getting a retractable pool enclosure made by Alukov much like the one in the photo below.

I did as much due dilligence as I could, which included but was not limited to getting quotes from several different manufacturers/dealers of different types of enclosures, checking wind and snow load in my area and county requirements, reading reviews on Houzz and FaceBook, getting drawings, and visiting a property owner in the PNW with a 10 year-old Alukov enclosure so I could see how they stand up to our climate. Once again, the concrete deck became a crucial focus as the foundation for this structure and not something one would want to try to address after enclosure installation.
In researching concrete companies, I was referred to the same local contractor (Tony at Absolutely Fine Concrete) by two parties who didn't know each other -- the owner of the Alukov enclosure I'd visited and the pool construction / maintenance company (KrisCo Pools) that did my pre-purchase inspection and later a one-on-one lesson on how to use/maintain my equipment, vacuum and adjust the water level in the pool, and test and balance my water. So, I contacted Tony to come out for a quote, had a second contractor (a friend of a friend) come out for a quote, and talked to a few others who either seemed skiddish about working around a pool or had other reasons they were not keen to come out for a quote.
Tony was the obvious choice based on his portfolio and track record and his connections with folks in the pool building industry in Seattle. We were initially slated to start the demolition May 1st until we ran into two or three snags: (1) We couldn't find a pool company to come out to put the pipes under pressure in the timeframe needed. This procedure is not in Tony's wheelhouse and not a step he was willing to skip given the risk of breaking a pipe during demolition. (2) When Krisco's expert came out to discuss the process and their availability with me and Tony, he noticed that there had been a second layer of tile glued over the top of the original tile, which meant the demolition process was most likely going to ruin the tile and mess up the plaster. So we now needed to find someone to re-tile the water line. (3) The existing plaster had been painted (at least once) and so it was highly recommended that the old plaster be chipped out and new plaster done. I could have taken a "wait and see" stance to see if the plaster would survive tile removal / replacement, but when I considered the logistics of doing a replaster a few years down the road with an enclosure already in place, it made the most sense to to do it now and be done with it.
Krisco was back up through August so it was looking like the whole project might be delayed until late summer, early fall or maybe 2025. Then, one of Tony's other pool contacts (Scott with the Gunite Company) wrapped up a big job in Bellingham a little early and had a window before his next big job (a 95' private pool new construction). So we were off to the races. Scott has turned out to be a godsend because he's been building pools for 30+ years, has a great personality, and I've learned a lot from him as we've worked through the quirks of my project. He's worked on a lot of pools in my local area and has a reputation for being transparent and more than fair.
Doing the tile and plaster increased the cost of the entire job by about 50% (half again as much as the concrete job) ... but I'm glad I committed to it. When we got the pool drained, I could see the paint was bubbling in a lot of places and likely covering up hidden plaster issues that would only worse with time and use. Also, with the mechanical failures of the old heater and pump, it's been great to have a PB who can help me with a good solution.
I've got lots of before, during and after photos and videos ... the one below shows the job after the old concrete was demolished and the plaster chipped out (done by two different vendors in parallel -- sharing the same dumpster) and after new concrete and coping pour was complete -- and after the waterline and step marker tile was laid but BEFORE plastering and refilling. Watching the plastering being done was like a cake being frosted - it was so cool to see the artistry involved!

The below photo was taken today. I'm still waiting for escutcheons for the new handrail. The new heater was fired up for the first time today and chemicals are about right! I'm looking forward to a swim as soon at the temperature's comfy (it's a chilly 60°F in Seattle today despite it still being August). The enclosure is slated for delivery and installation in late October / early November. Stay tuned. I hope to report on how well it retains heat. It will definitely cut down on bugs and debris in the pool!

In review, my pool's "face lift" that included
- demolish a cracked and shifted aggregate deck/coping and pour a new stamped concrete deck with separately poured coping
- the footprint for the enclosure is level with concrete outside the enclosure sloping away for drainage
- a rebar grid that is fully grounded is under the slab and connects to the handrail sockets
- a bit of re-grading was done between the house and pool to remove the need for a step down from the prior patio to the pool deck and a french drain was added to handle patio runoff toward the pool enclosure
- a beautifully organic beachy wave pattern in a mid-tone color was created to make a forked path from the back door to the pool or from the back door to the driveway
- coping was visually defined for safety and aesthetic interest with a darker concrete dye
- chip out previously painted plaster, replastered with classic white
- remove two layers of waterline tile and replaced with Fujiwa 6x6 tile and add step marker tile where there was none
- I got creative with the step marker tile using two different colors of tile pebbles -- intermingling a "streak" of gold diagonally on each step starting at the top left on the top step, crossing the middle step in the middle, and ending on the right of the bottom step
- This involved cutting the 12"x12" pebble "mats" into three roughly 4" strips and laying them end-to-end the length of the steps and then mpeeling blue tiles off the mesh backing material wherever we wanted to insert a gold tile that was peeled off its backing
- My 23 year old son and I worked for about 8 hours (one evening and the next morning) manually laying this out for each step and using blue masking tape to secure the "loose" gold tiles in place. This is not for the faint-of-heart and requires a pool tile person willing to go the extra mile!
- We LOVE the result ... it's truly unique!
- pour a deep end sitting bench that doubles as a step exit and removed deep end metal ladder - the bench has the same pebble marking as the steps

- replace shallow end handrail with new (and properly grounded) S.R. Smith Artisan handrail, and (6) replaced failed/disconnected incandescent uderwater light with Pentair Intellibrite multicolor LED pool light.
- Replaced old 200 BTU NG heater, which sprang a leak just as renovations started and we were putting skimmer and drain pipes under pressure) with new Raypack 406 NG heater. Ugh!
- This was not caused by anything The Gunite company did to put pipes under pressure .... just a "Murphy's Law" random event that the rusted out heater didn't last another year as I was hoping.
- The new heater will be way more fuel efficient so a blessing in disquise.
- Replaced old Haywood pump,(which failed when we restarted it up for the first time after the pool was re-filled. We'd disconnected it to pressurize the skimmer and drain pipes ... and to replace a leaky seal. When it was started back up, it made a terrible noise and the motor got burning hot. The new variable speed pump is way better and meant we could get rid of the old pump timer in the process.
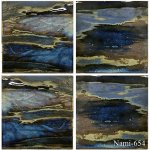

