- Jun 17, 2019
- 58
- Pool Size
- 18000
- Surface
- Plaster
- Chlorine
- Salt Water Generator
- SWG Type
- Pentair Intellichlor IC-40
My pool is in direct sunlight 100% of the time during daylight hours, so I've been wanting to add some shade over the pool as my pool temp from July through September can reach as high as 95 degrees. Screen enclosures are much too expensive in SE Texas, so I decided to install shade sails to try to help provide some solar relief. After finally getting approval for the project from my HOA board of directors at the end of July, I was able to start the project this past Friday and complete it in two days.
I installed two 24-ft equilateral triangle sails supported by 6x6x14' pressure treated pine posts, a strategically placed 6" eye lag bolt into my 2nd floor joists, and varying lengths of 2000# WLL chain. Here are some photos of the project.
This first photo shows the tow-behind auger I used to dig the three post holes. I wanted to go 48" deep, but I just couldn't get there with this auger and stopped at 42". I would have had to rent a skid steer with auger attachment to go deeper. Pro tip: If you have hard soil, use a smaller auger to get to the desired hole depth, then a larger auger to get to the desired hole width. I started with a 6" auger and finished with a 10" auger. And I also found out that a powered auger drills a hole 2" larger than the auger. So my 10" auger provided a 12" wide hole - exactly what I wanted.

The next two photos show the posts in the holes before being leveled and set using Secure Set instead of concrete. The posts were delivered as 6x6x16', but since my connection points were only 9' above ground, I cut off 2 1/2' while the poles were still on the ground, making the poles much easier to muscle into the hole. I also mounted the eyebolt (3/8"x6" stainless steel) while the poles were on the ground too. This made the overall above ground pole height 10' after accounting for the 3 1/2' in the ground.
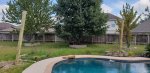
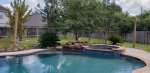
As I mentioned above, I did not use concrete to set the posts; instead I used a product I found online called Secure Set (www.secureset.net). This is a foam product that ships in two liquid parts and is mixed like epoxy, then quickly poured as a soupy liquid into the post hole. The mix begins to rise as foam in less than a minute, and the hole was completely filled in about 2 minutes. The cool part about this stuff is that the pole braces can come off in 5-10 minutes, and the foam is TOTALLY cured and ready for tension in one hour. My project took 3 gallons (1 1/2 gallons of each part). So instead of moving over a ton of concrete mix (Quikrete website indicated EIGHT HUNDRED POUNDS PER HOLE!), I only had to move a few ounces of mix at a time. Since it expands and compresses against the soil (think of a blood pressure cuff) until it can't expand anymore, it is ideal for highly compressed soil like the hard clay we have in SE Texas. After applying full tension to the sails (approaching 1000 pounds), the posts are still perfectly plumb. The cost once you get to this volume is cheaper than concrete. Highly recommended. The photo below shows the foam in its final risen state; I have not gone back and trimmed the foam or backfilled the dirt up to the post.

At the house, I used a 1/2"x6" eye lag bolt as the final attchment point. I was able to determine where my 2nd floor plywood subfloor began, so I predrilled through the Hardiplank, sheathing, floor joists and into the subfloor plywood the full 6 inch depth. I think the side of the house would fall down before the eyebolt would come out!

After the posts were set, it was just a matter of attaching each sail to the posts and to the house using 2000# WLL chain and turnbuckles, getting the chain as tight as possible by hand while leaving the turnbuckles totally extended. This is the first sail before being tensioned.

I then used a ratchet strap to put tension on each leg of the sail (and moving the chain links up while doing so), until the strap was as tight as I could get it. I then used the turnbuckle to finish the tensioning. This photo is of both sails almost fully tensioned.

Although the temp has not yet dropped from the 90 degree mark it was at when I started the project Friday morning, the comfort level just moving from the sun to under the sails makes the water much more tolerable. We are expecting rain here the next couple of days, so that will hopefully lower the water temp a bit and I can really see if it's going to make the difference I believe it will.
I have a video of the finished project, but it is too large to upload, so I'll try to edit it down some and post it later.
I would estimate that I spent about $650 on this project, including the auger rental. The only thing I would do differently would be to rent the skid steer auger.
Let me know what you think!
I installed two 24-ft equilateral triangle sails supported by 6x6x14' pressure treated pine posts, a strategically placed 6" eye lag bolt into my 2nd floor joists, and varying lengths of 2000# WLL chain. Here are some photos of the project.
This first photo shows the tow-behind auger I used to dig the three post holes. I wanted to go 48" deep, but I just couldn't get there with this auger and stopped at 42". I would have had to rent a skid steer with auger attachment to go deeper. Pro tip: If you have hard soil, use a smaller auger to get to the desired hole depth, then a larger auger to get to the desired hole width. I started with a 6" auger and finished with a 10" auger. And I also found out that a powered auger drills a hole 2" larger than the auger. So my 10" auger provided a 12" wide hole - exactly what I wanted.

The next two photos show the posts in the holes before being leveled and set using Secure Set instead of concrete. The posts were delivered as 6x6x16', but since my connection points were only 9' above ground, I cut off 2 1/2' while the poles were still on the ground, making the poles much easier to muscle into the hole. I also mounted the eyebolt (3/8"x6" stainless steel) while the poles were on the ground too. This made the overall above ground pole height 10' after accounting for the 3 1/2' in the ground.
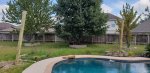
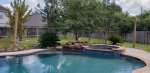
As I mentioned above, I did not use concrete to set the posts; instead I used a product I found online called Secure Set (www.secureset.net). This is a foam product that ships in two liquid parts and is mixed like epoxy, then quickly poured as a soupy liquid into the post hole. The mix begins to rise as foam in less than a minute, and the hole was completely filled in about 2 minutes. The cool part about this stuff is that the pole braces can come off in 5-10 minutes, and the foam is TOTALLY cured and ready for tension in one hour. My project took 3 gallons (1 1/2 gallons of each part). So instead of moving over a ton of concrete mix (Quikrete website indicated EIGHT HUNDRED POUNDS PER HOLE!), I only had to move a few ounces of mix at a time. Since it expands and compresses against the soil (think of a blood pressure cuff) until it can't expand anymore, it is ideal for highly compressed soil like the hard clay we have in SE Texas. After applying full tension to the sails (approaching 1000 pounds), the posts are still perfectly plumb. The cost once you get to this volume is cheaper than concrete. Highly recommended. The photo below shows the foam in its final risen state; I have not gone back and trimmed the foam or backfilled the dirt up to the post.

At the house, I used a 1/2"x6" eye lag bolt as the final attchment point. I was able to determine where my 2nd floor plywood subfloor began, so I predrilled through the Hardiplank, sheathing, floor joists and into the subfloor plywood the full 6 inch depth. I think the side of the house would fall down before the eyebolt would come out!

After the posts were set, it was just a matter of attaching each sail to the posts and to the house using 2000# WLL chain and turnbuckles, getting the chain as tight as possible by hand while leaving the turnbuckles totally extended. This is the first sail before being tensioned.

I then used a ratchet strap to put tension on each leg of the sail (and moving the chain links up while doing so), until the strap was as tight as I could get it. I then used the turnbuckle to finish the tensioning. This photo is of both sails almost fully tensioned.

Although the temp has not yet dropped from the 90 degree mark it was at when I started the project Friday morning, the comfort level just moving from the sun to under the sails makes the water much more tolerable. We are expecting rain here the next couple of days, so that will hopefully lower the water temp a bit and I can really see if it's going to make the difference I believe it will.
I have a video of the finished project, but it is too large to upload, so I'll try to edit it down some and post it later.
I would estimate that I spent about $650 on this project, including the auger rental. The only thing I would do differently would be to rent the skid steer auger.
Let me know what you think!